Traceability
Traceability Traceability in Monitor ERP is all about being able to trace a specific serial number or a batch in each step it is being processed, as of when a part or a material arrives with you from a supplier. Traceability is also about stating what is withdrawn from and what is added to stock, so it is then possible to trace from customer order, via manufacturing order to purchase order. But it is also about being able to trace the other way around; from purchase order via manufacturing order to customer order. is all about being able to trace a specific serial number or a batch in each step it is being processed, as of when a part or a material arrived to you from a supplier. Traceability is also about stating what is withdrawn from and what is added to stock, so it is then possible to trace from customer order, via manufacturing order to purchase order. But it is also about being able to trace the other way around; from purchase order via manufacturing order to customer order. You should be able to make such tracking regardless of the level in the process. To make the traceability work, there are also requirements regarding how to label/mark and document in all steps of the process.
The purpose of traceability is in the end to minimize the number of products which must be recalled if a nonconformity should occur. This is done by having a secure and detailed traceability through all levels of the processing.
There are two different levels of traceability in Monitor ERP. This is traceability at batch level and traceability at serial number level.
Terms | Explanation |
---|---|
Serial number![]() |
Serial numbers are unique for one (1) entity, for example, a circuit board. If there are 10 circuit boards there are 10 entities with unique serial numbers. An entity (serial number) is unique in Monitor ERP in combination with its part number. This way it is possible to handle when there are two suppliers who have entered the same serial number but for different part numbers. Serial numbers can be used for both purchased and manufactured parts. Serial numbers may have a maximum of 15 characters. |
Batch number![]() |
A batch number is unique for a batch/lot of same things. A batch number can also be the same for multiple entities which have own serial numbers. For example, if the 10 circuit boards are all manufactured at the same time, they might be given a batch number by the supplier which is the same for all 10 circuit boards. |
Charge number![]() |
A charge number is normally an identification you receive from the supplier for the batch or the lot which was manufactured by the supplier. A charge number can also be entered afterwards for a serial number or a batch number in the Serial number/Batch![]() |
Activate traceability for parts
In the Part register you can activate traceability for parts by using the setting Traceability.
There are three different ways to apply traceability for parts, as described below.
- Batch – This can be configured both for manufactured and purchased parts. When arrival reporting to location you enter a batch number for the location to which the arrival should be made. Once batch traceability has been activated you can also activate the setting Apply best-before date. It will then become mandatory to select a best-before date when you create the batch, for example at arrival reporting.
- Serial number – This can be configured both for manufactured and purchased parts. For manufactured parts the serial number is loaded from the number series when the manufacturing order is created. For purchased parts the serial number is entered at the arrival reporting. When arrival reporting to location you add a serial number for the location to where the arrival is made. The arrival reporting is made per entity and location.
- Serial number (only withdrawal) – This option can only be selected for purchased parts. It is used for material which should be possible to trace and which is included in manufactured parts with the option Serial number set as traceability. The serial number for the included material is created when it is tied to the manufactured part's serial number during the actual reporting. This means that the serial number is not registered to a location in the warehouse/stock, but only in the serial number register.
If there is a part balance when you activate the traceability as Batch or Serial number you will be shown a warning about there being a balance missing a serial number/batch number. This should then be fixed by adding the serial number/batch number to existing locations and balances in the Stock count procedure.
If the part balance is negative then it is not possible to activate traceability. It is also not possible to activate traceability of the Serial number type for a part if the part is included as material in an active manufacturing order.
Parts with traceability must be stock updated. This means that parts of the type Fictitious or Service never are traceable.
Create new locations at arrival
With the system setting Create new location at arrival you determine if new locations should be automatically created during arrival reporting, either for all parts regardless of traceability or only for traceable parts.

When this setting is activated you can use the system setting Name new locations at arrival to choose if the new locations should have no name (empty by default, you can enter a name), eight asterisks (********), or a consecutive number (in the form of *1001*, *1002* etc.).
Random stock location
The setting Random stock location in the Part register determines if the locations created for a part should be a random stock location or not. This means that such a location will be removed from the part if the balance would go down to zero (0) at a withdrawal.
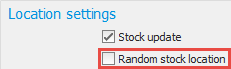
Other stock reporting
The procedures Move stock balance, Stock count, Stock count in list, and Direct stock reporting (called Unplanned stock movements in the previous generation of MONITOR) handle all materials with traceability.
In the procedures Undo arrival reporting, Undo reporting, and Undo delivery reporting traceable parts are handled. A serial number or a batch can for example be deleted if the arrival reporting creating the serial number/batch is undone.